Oil and Gas
Oil and Gas
ANSYS applications in the oil and gas industry
The challenges facing the oil and gas industry boil down to using technology to manage the risks associated with finding and producing resources at a reasonable cost. The industry is under enormous pressure from the recent fall in prices. At the same time, advances in the seismic technology used in exploration have been essential in finding hydrocarbons in all types of formations. The challenge today is to develop these fields safely, reliably and sustainably. The industry must invest in the development of new technologies to reduce costs and ensure profitability, while meeting increasing regulatory requirements.
We provide the most advanced software and a network of technical experts who work with oil and gas customers around the world.
Our brochure shows recent examples of the best ANSYS solutions and simulations performed for the oil and gas industry.
Brochures
ANSYS Oil & Gas applications
CADFEM HPC
ANSYS 2024 R1 capabilities chart
ANSYS applications in the oil and gas industry
The challenges facing the oil and gas industry boil down to using technology to manage the risks associated with finding and producing resources at a reasonable cost. The industry is under enormous pressure from the recent fall in prices. At the same time, advances in the seismic technology used in exploration have been essential in finding hydrocarbons in all types of formations. The challenge today is to develop these fields safely, reliably and sustainably. The industry must invest in the development of new technologies to reduce costs and ensure profitability, while meeting increasing regulatory requirements.
We provide the most advanced software and a network of technical experts who work with oil and gas customers around the world.
Our brochure shows recent examples of the best ANSYS solutions and simulations performed for the oil and gas industry.
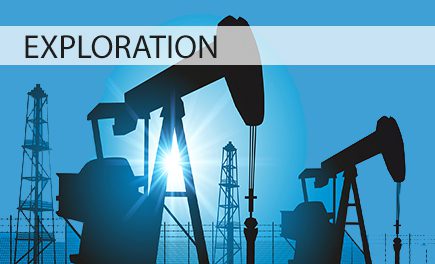
Schlumberger: Cost-Effective Deployment of Oil Well Tubing
Accurate nonlinear structural mechanics simulation enables the prediction of the behavior of the tubing string when it undergoes complex buckling, which often results from fluid injection operations. The latest simulation methods allow engineers to design tubing strings and downhole tools capable of handling the most difficult wells to drill today.
Schlumberger, the world’s leading provider of technology solutions for the oil and gas industry, conducts quality tests to obtain important measurements such as flow rate and bottom-hole pressure to characterize oil reservoirs.
Schlumberger has developed a new approach using ANSYS Mechanical BEAM188, which provides a more accurate method for simulating helical buckling in a well test chain sealed in a packer.
Schlumberger Limited is a multinational company providing oilfield services and equipment.
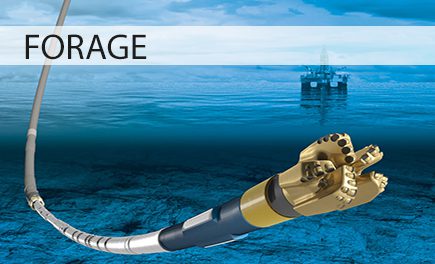
Cognity Ltd: Design of the First Steerable Conductor
One of the biggest challenges in offshore drilling is the precise placement of the conductor casing to help maximize production at the field.
Engineering company Cognity Limited solved this problem by developing a steerable conductor that can provide real-time accurate positioning.
Using ANSYS Mechanical on the ANSYS Workbench platform, engineers at Cognity doubled the load capacity of the steering mechanism, allowing the conductor to be maneuvered in very deep soils.
Cognity’s design is the first to allow the conductor to be steered in real time from the drilling platform, enabling highly precise control of the final position. The advantages of such a system include possible increases in production and reduced drilling costs by eliminating drilling slots.
Cognity is a consulting company specializing in mechanical design, particularly for the oil and gas market. The company uses ANSYS software to save time and money from the early stages of the design process.
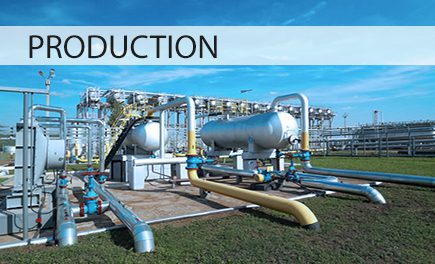
Natco Group Inc.: Flow Inside a Gas and Oil Separator
An offshore platform can undergo six degrees of wave motion (shock wave, heave, roll, yaw, pitch, and sway). When combined, these motions act to mix gas, oil, and water in the separator, which is counterproductive to the separation process.
The transient sloshing of oil, gas, and water inside a separator was simulated using the Volume of Fluid (VOF) model in ANSYS FLUENT. Both normal and stormy sea conditions were studied.
CFD simulations were conducted with and without baffles to study their effect on sloshing and mixing. The results showed that the baffles were not able to substantially suppress sloshing and the resulting oil-gas mixture.
In fact, if the baffles are not placed correctly, they could worsen the fluid short-circuiting in the separator. A new baffle system was then proposed that included strategically placed perforated plates.
NATCO Group is a company that provides processing equipment, systems, and services used in oil and gas production.
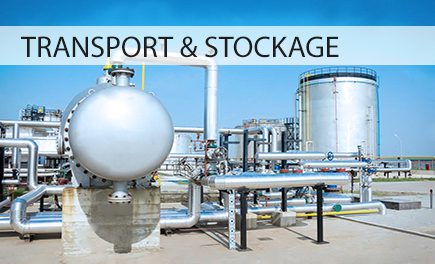
ITMA Materials Technology: Simulation of a Storage Tank
ITMA Materials Technology – a Spanish company focused on applied research and development in materials science – uses multiphysics simulation to optimize material performance.
An engineering team at ITMA used ANSYS CFD and ANSYS Mechanical software to conduct a fatigue analysis of a storage tank. Since this tank must operate reliably under extreme temperature changes, ensuring its structural integrity is essential.
Using the integration capabilities of ANSYS Workbench, ITMA researchers first performed transient analyses of the tank’s startup and shutdown cycles in ANSYS CFX and then transferred the temperature distributions to ANSYS Mechanical.
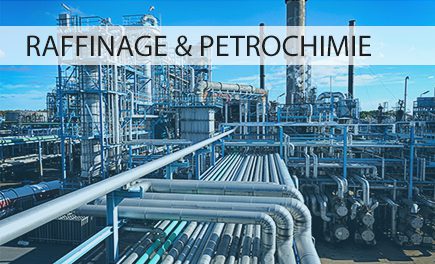
Fuel Reformers Optimization
Fuel reformers and cracking furnaces contain a combustion chamber in which heat is generated by burners. This heat is transferred to serpentine tubes carrying process steam.
These tubes must evenly heat the flow for the cracking to be efficient. To achieve maximum efficiency and eliminate hot spots that could lead to tube fouling and failure, equipment designers must understand the interactions between 3-D combustion in the furnace and the 1-D exothermic chemical reaction in the process tubes.
The ANSYS CFD software uses a channel model to simulate complex reformers and cracking furnaces more quickly by coupling the desired 1-D and 3-D reactions in a single integrated simulation.
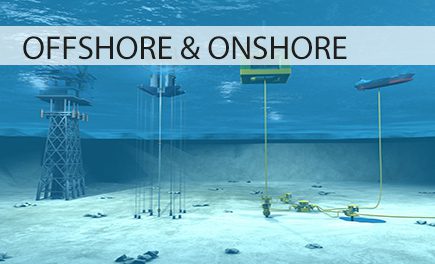
Multiphysics Analysis of Equipment Launch
Accurate simulation of the movement and behavior of offshore and subsea structures during equipment launch requires a comprehensive set of solutions – including hydrodynamics, fluid mechanics, and structural mechanics.
ANSYS comprehensive solutions for fluid-structure interaction simulations help engineers understand and optimize the successful launch of complex equipment.
Recently, the results of a fluid-structure interaction approach using ANSYS solutions were demonstrated on a 58-ton subsea manifold.
Transient simulations were performed to calculate fluid forces, which were then used to calculate the structural response of the manifold in the splash zone.